Ganelec
Diamond Dotted Paper
Diamond Dotted Paper
Couldn't load pickup availability
Diamond Dotted Paper is made of Kraft paper coated with heat-curable epoxy resin. The epoxy adhesive is applied to both sides of the paper in a diamond pattern consisting of 9.5mm x 9.5mm diamonds with 15.9mm center spacing.
The Diamond Dotted Paper is to be used in oil-immersed transformers for the insulation between coils. On the insulation layer, there is a layer dotted epoxy resin that will be changed with high temperatures. The material has good inertia, is dry and has no conglutination at normal temperature (below 30℃).
The Diamond Dotted Paper (DDP) will make the electric conductor "felt up" as a hard unit under high temperatures by its internal latency substance. When the temperature rises to 90℃, the Diamond Pattern Paper (DDP) begins one-off thaw and then one-off solidification. When kept at 90℃ for 90 minutes, the epoxy resin pastes onto the neighbouring cable and paper safely. The felt intensity is as high as 70 psl at 100℃.
(The value at least is equal to 0.450Mpa) (IEC standard).
We can also produce width of DDP according to the customer’s requirements.
Material name
Diamond Pattern Paper, Diamond Dotted Insulating Presspaper, Diamond Dotted Paper, Ddp, Double Sided, Diamond Pattern Paper, Ddpp, Dprcp, Diamond Pattern Resin Coated Paper, Varnished Paper Epoxy, Adhesive Diamond Paper etc.
Typical values
Thickness (mm) | 0.08, 0.13, 0.18, 0.25, 0.38, 0.50 |
Thickness tolerance +/-mm (+/-10%) | 0.005, 0.013, 0.018, 0.025, 0.038, 0.05 |
Width (mm) | 500, 625, 810, 960, 1000, 1100, 1219, 1300 (We can also produce width of DDP according to the customer’s requirements) |
Width tolerance (mm) | +/-5, all thickness |
Reel diameter (mm) | 300-360 |
Can core diameter (mm) | 76+/-2 |
Apparent density (g/cm3) | 0.9 to 1.1, all thickness |
Moisture content (%) | 6.0 to 10.0, all thickness |
PH of aqueous extract | 6.0 to 8.0, all thickness |
Ash content (%) | 1% maximum |
Elongation MD (%) | 4 |
CMD (%) | 9 |
No-pollution oil of transformer | Non-pollution |
Coating thickness per side (mm) | 0.006 to 0.012 |
Tear strength (g) - machine direction | 55, 100, 140, 220, 410, 440 |
Tear strength (g) - cross machine direction | 70, 145, 210, 370, 600, 700 |
Tensile strength (N/mm2) - machine direction | 90, 90, 80, 90, 92, 95 |
Tensile strength (N/mm2) - cross machine direction | 30, 25, 35, 35, 35, 35 |
Mullen burst strength: min (Psi) | 40, 65, 90, 150, 200, 300 |
Dielectric breakdown (volts/layer; dry test) | 750, 1300, 1700, 2100, 3000, 3300 |
Dielectric breakdown (kilovolts/layer; oil test) | 5.5, 8.5, 10.5, 14.0, 20.0, 23.5 |
Bond strength (Psi) | Min 40 (tested at 100 degrees) |
Kpa | 450 |
Catalogue
GANELEC/OUCO Transformer Equipment Accessories Catalogue - pg 36
Share
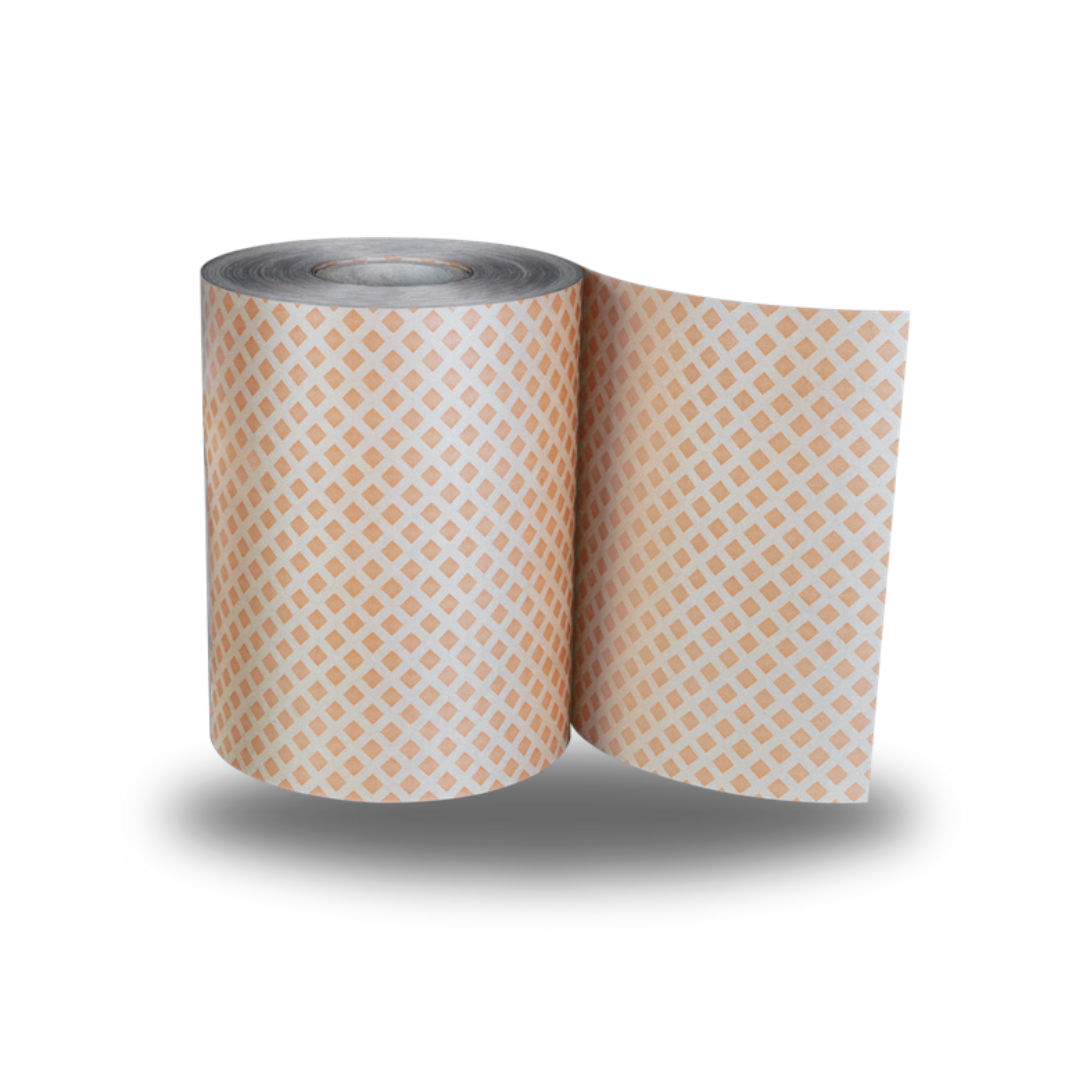